What to Look for in an Automated Bottle Capping Machine?
Selecting the right automated bottle capping machine is a critical decision for ensuring efficiency, product integrity, and safety in production lines. Choosing the wrong machine can lead to significant waste, including product loss, increased downtime, and additional costs associated with replacing defective products.
Co-packers or manufacturers must consider several technical specifications and features to optimize operations, particularly when handling a diverse range of containers such as bottles, jars, vials, canisters, and more, as well as various cap types including ROPP, twist-off, screw caps, trigger caps, air pump caps, screw-on caps, and snap-on caps. This article provides an in-depth analysis to help you make an informed choice.
Reliability
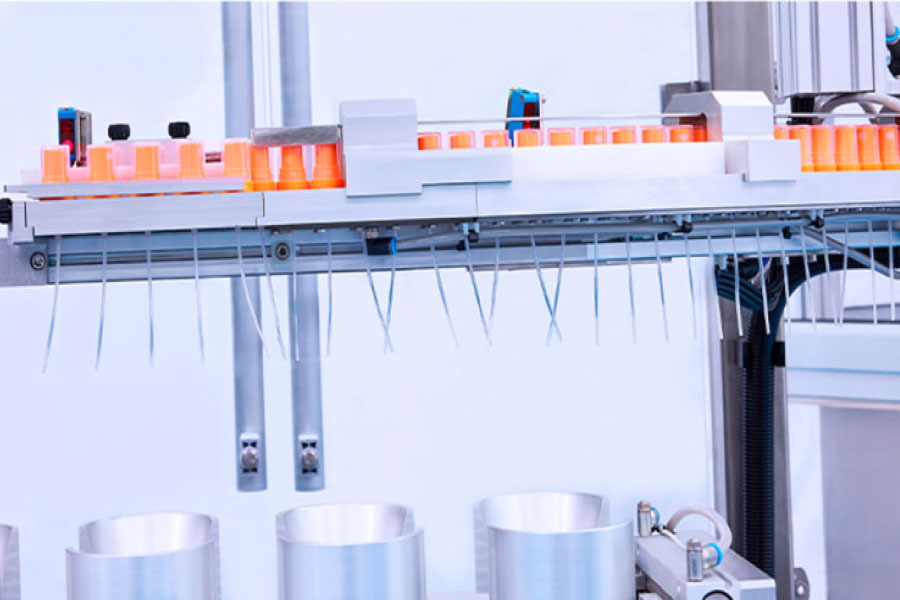
Precision Engineering and Consistency
Reliability is of paramount importance in capping operations. An effective capping machine should offer precise control over the capping process to ensure consistent sealing across various container types such as vials, jars, canisters, bottles, and more. Top innovative technologies that will ensure precision capping and operational consistency to look for:
- Servo-Driven Cam Design: This advanced technology provides precise torque control and operational consistency, which is essential for managing closures such as screw caps, ROPP caps, twist-off caps, trigger caps, pump caps, and snap-on caps.
- Continuous Robotic Fast Cappers: These innovative machines use robotics for fast, efficient capping, significantly increasing production speed while maintaining precision. A robot manipulator for a continuous motion capping machine features a robotic arm that moves in multiple axes, ensuring accurate cap placement as bottles flow seamlessly through the capping process. This design minimizes the risk of misalignment, enhancing overall reliability in the production line. Watch a Continuous Robotic Fast Capper in action here!
Speed
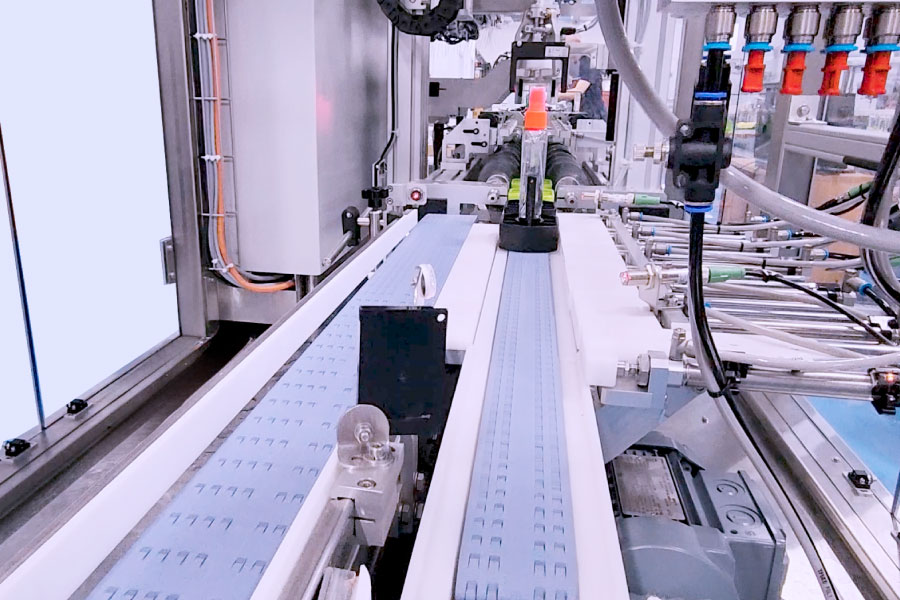
Optimizing Production Rates
The operational speed of a capping machine must align with your production line’s throughput requirements. Factors to evaluate include:
- Capping Speed: Assess the machine’s capacity (caps per minute) and ensure it meets your production demands. Advanced models often feature adjustable speed settings to accommodate fluctuating production volumes, making them suitable for bottles, jars, canisters, vials, and handling different cap types.
- Integration with Conveyor Systems: A capping machine should seamlessly integrate into existing high-speed conveyor systems. Compatibility ensures that production flows smoothly without bottlenecks, which can affect overall efficiency.
Fit into Existing Systems
Seamless Integration
Before acquiring a capping machine, it is essential to evaluate how well it will integrate with your existing production line. Key considerations include:
- Multi-Container Modular Design: A modular machine allows for easy adaptation to different container and cap types. This flexibility is crucial for manufacturers producing multiple products with varying packaging requirements, such as cosmetics, food and beverage, and chemical manufacturers.
- Technical Compatibility: Ensure that the machine’s dimensions and operational requirements align with your current system, including the ability to interface with existing line control systems.
Premium Components
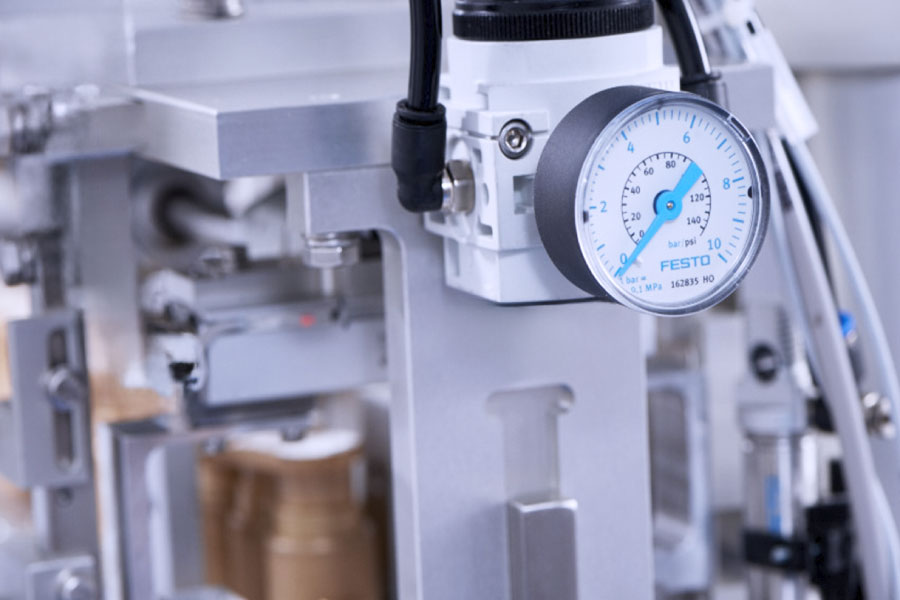
Investing in Quality for Long-Term Success
Having premium components in your automated bottle capping machine is essential for optimal performance and reliability. High-quality parts contribute to:
- Durability: Premium components withstand the rigors of high-speed production, reducing the frequency of replacements and maintenance.
- Fast Shipping: Reputable manufacturers often have ready-to-ship inventory of high-quality parts, ensuring minimal downtime during repairs or upgrades.
- Enhanced Performance: Quality components lead to more efficient operation, ensuring consistent capping results and reducing the risk of product defects.
Ease of Use
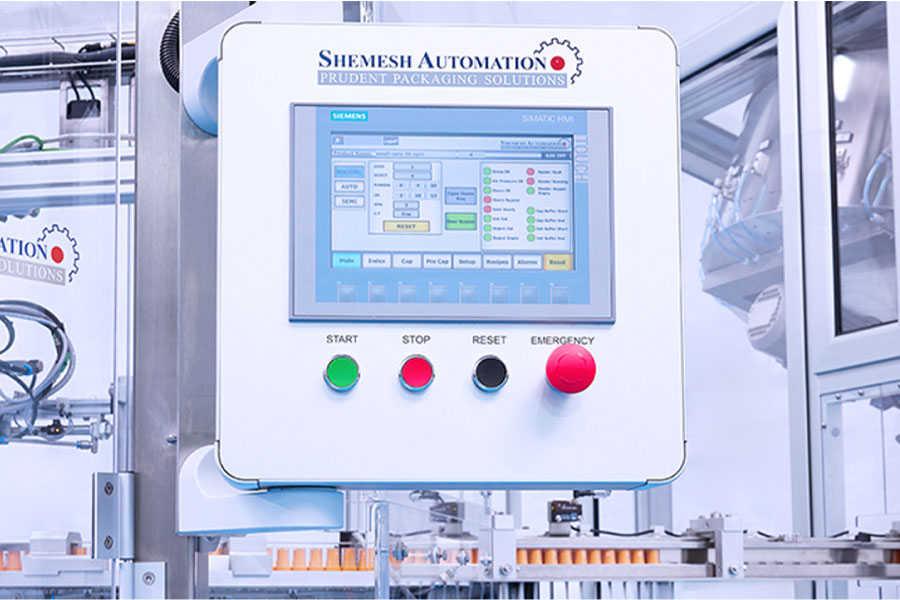
User-Friendly Interfaces
An intuitive user interface significantly impacts operational efficiency and training time for operators. Consider the following features:
- HMI Touchscreen Controls: Modern machines often include touchscreen panels that provide real-time performance data and diagnostics, allowing operators to adjust settings easily and monitor production.
- Minimal Change-over Setup Time: Change-over to a new product with ease by touching a recipe in the HMI to on-click digitally adjust the new setup parameters.
- User-Friendly Software: An effective software interface can facilitate quick operator training and provide remote monitoring capabilities for troubleshooting.
Ease of Maintenance
Minimizing Downtime
Maintenance is a critical aspect of any automated capping machine. Key features to consider include:
- Modular Components: Machines designed with modular components simplify maintenance tasks, allowing for quick replacement without extensive downtime. This design is particularly valuable in high-output environments where every minute counts.
- Support and Documentation: Ensure that the manufacturer provides comprehensive support, spare parts availability, and detailed user manuals for troubleshooting.
Safety
Ensuring Operator Protection and Compliance
Safety features in capping machines are critical for protecting operators and ensuring compliance with industry standards. Look for machines that include:
- Emergency Stop Mechanisms: These should be easily accessible, allowing operators to halt operations quickly in case of an emergency along with E-stop buttons and safety interlocks wired through a safety controller.
- Safety Guards and Interlocks: Incorporating protective guards and safety interlocks prevents accidental operation during maintenance or setup, ensuring operator safety.
Quality Control
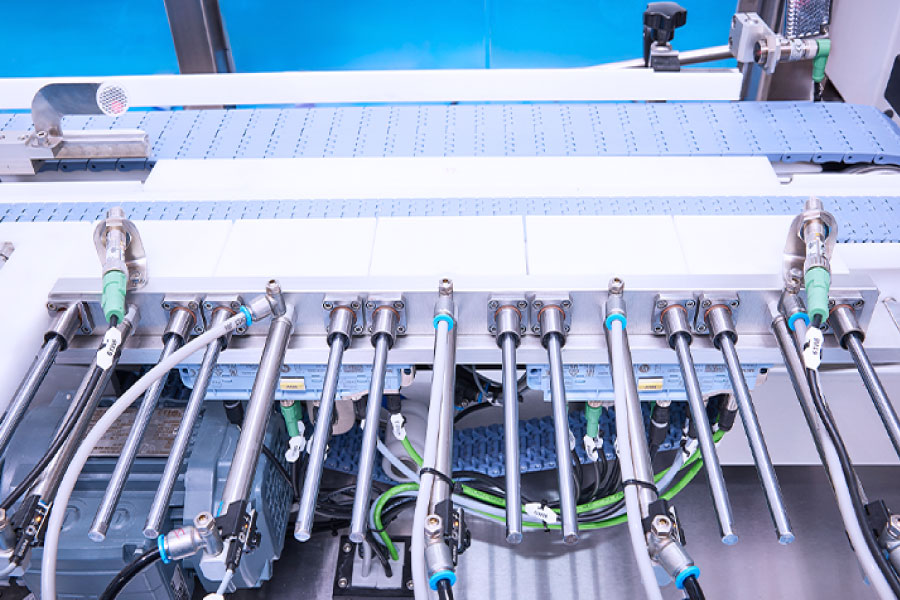
Ensuring Product Integrity
Integrating quality control mechanisms into your automated capping machine is essential for maintaining product integrity. Key considerations include:
- Quality Control Systems: Machines should incorporate sensors to verify cap placement and closure integrity, ensuring that every container is properly sealed, whether using screw-on caps, snap-on caps, trigger caps, ROPP caps, twist-off caps, or pump caps.
- Digital Servo QC System: An advanced digital servo quality control system will detect an unsatisfactorily capped bottle and reject the incorrect item. Additionally, a pick-and-place method ensures accurate placement of screw or twist-off caps, while a clipping method allows for precise snap-on and push-pull capping.
- Adjustable Torque Settings: Precise torque adjustments are critical for different cap types, allowing for customization based on the specific requirements of various containers.
Conclusion
Selecting the right automated bottle capping machine requires careful consideration of its reliability, speed, integration capabilities, ease of use, maintenance requirements, safety features, and quality control mechanisms. By focusing on these technical aspects, including the importance of premium components and advancements like Continuous Robotic Fast Cappers, you can ensure that your capping machine meets your production needs for bottles, jars, vials, canisters, and other packaging types, ultimately enhancing your operational efficiency.
For more information on how to choose your Automated Packaging Machinery, contact us for free advice and see how we can help in your decision-making process.
Join us on LinkedIn to stay updated with our latest news and discover our innovations in filling, capping, and sealing solutions.