If you’re looking to upgrade your liquid filling machinery, or even starting your first line, it’s likely the following considerations will be weighing on your mind:
- Filling speed
- Filling capacity
- Machine size
- Downtime
- Accuracy
However, there is one vital factor that could impact all of the above, and more, which you may not yet be considering – the filling mechanism utilised by the machine.
Not all volumetric liquid fillers are created equal
Volumetric liquid filling machinery is known for its high accuracy levels and versatility when it comes to filling various viscosities and particulates. There are a number of varieties of Volumetric filling methodologies available though – including Servo Driven piston fillers, Mechanical Cam fillers and pneumatic piston fillers.
Servo-Driven Piston Fillers
Servo-driven piston liquid filling machinery is known for its ability to precisely control the amount of liquid that flows out of their dispensing nozzles. The machine’s programme/software tells the servo piston filler how long to engage the piston and at specific, customisable speeds. Together, the technology/software and hardware ensure that the volume deposited into each container is precise, and uniform.
Shemesh’s STRATUM liquid filling machine is an example of servo-driven piston technology. STRATUM offers +/-0.25% of liquid volume accuracy. It is also capable of handling a wide range of viscosities from 1 to 500,000 Centipoise (water is at 1, peanut butter is at 250,000).
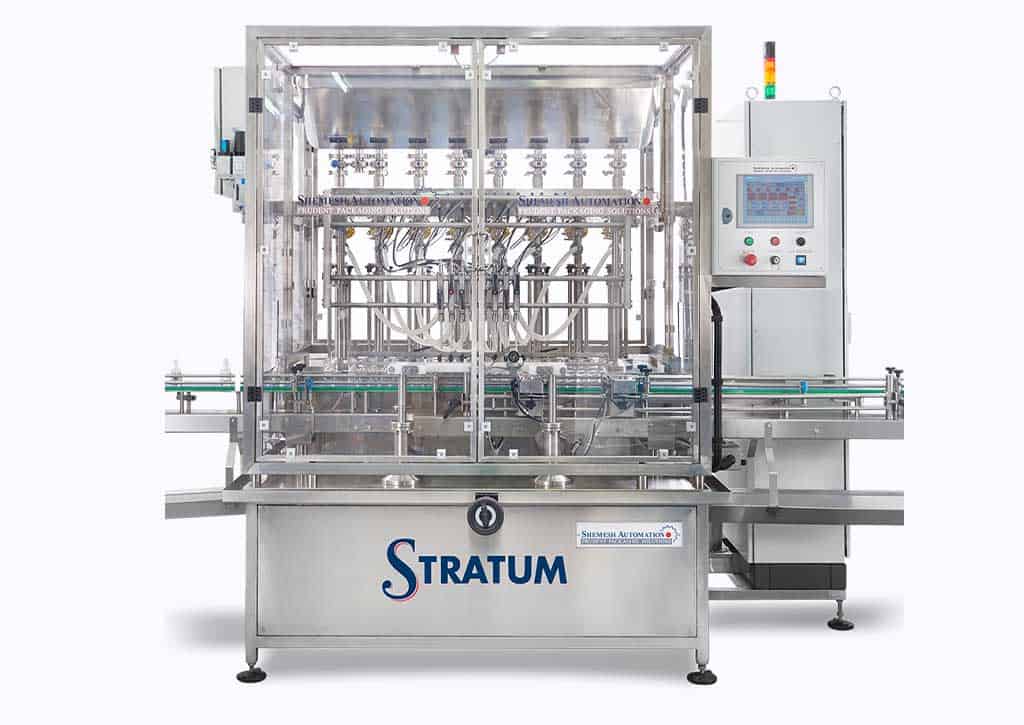
Mechanical-CAM Piston Fillers
As with servo-driven piston fillers, mechanical-CAM liquid filling machinery allows for precise control over filling speeds and volumes.
However, the added bonus is that the CAM mechanism allows greater force to be applied to the pistons, making quick and easy work of high viscosity liquids.
When it comes to ultra-viscous liquids (peanut butter for example) our ASTERRA mechanical CAM Rotary piston filling machine really comes into its own. Every bit as accurate as the STRATUM, ASTERRA’s mechanical CAM mechanism is able to apply additional force to the filling pistons. This allows for high speeds to be maintained consistently at ultra high viscosities.
ASTERRA also offers improved accuracy – when compared with Pneumatic Piston filling machines – as the mechanical CAM design does not rely on auxiliary air pressure – which can vary – to drive the filling mechanism.
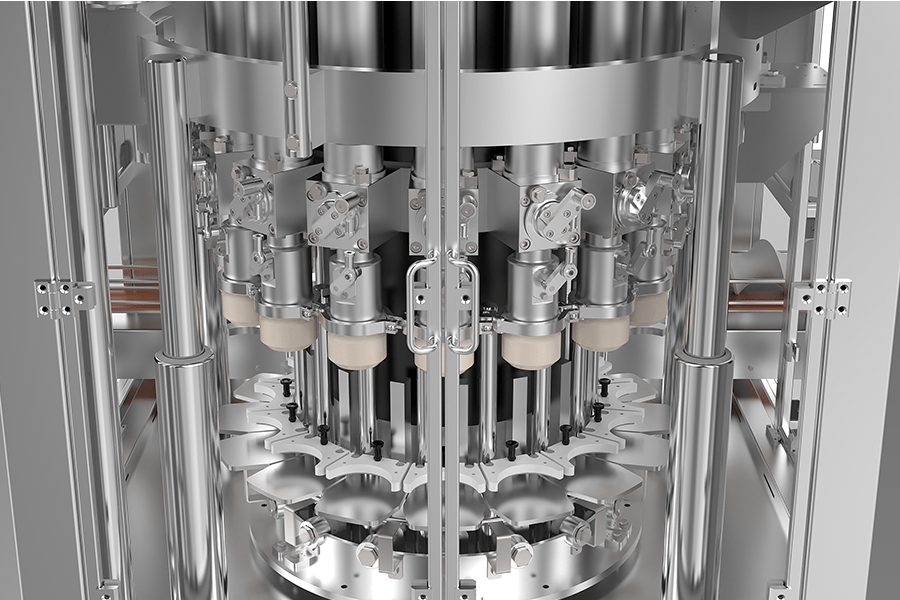
Rotary piston machines (ROPIMA) offer a continuous filling operation, whereas linear equivalents are stop-start. This allows rotary piston liquid filling machinery to handle higher volumes and maintain filling consistency.
Rotary piston fillers are also known for their flexibility when it comes to product changeover.
There is a vast array of rotary piston filling mechanisms, including Single Rotation Machines (SIM), Planetary Rotation Machines (PLM) and Rotating Piston Machines (ROM) which all offer slightly different methods of piston rotation.
You can read more about them here:
Pneumatic Piston Fillers
This type of technology is used for filling tubes and other open containers with high-viscosity fluids such as creams, gels etc. But requires separate compressed air to operate. The principle of the method is that the cylinder runs in reciprocating and linear motions to drive the piston and generate the suction and thrust which draws and pushes the liquid/product.
Adjustable filling speeds – more important than you might think!
Pneumatic Piston filling machines are limited by the fact that their speed profile is fixed throughout the cycle.
If the product you are filing is prone to foaming or splashing, or your containers are not uniform in shape (ie, they taper at the top, like a sauce bottle) you could be throwing product and money down the drain by opting for a Pneumatic Filler rather than a Servo-Driven or Mechanical Cam Rotary filler.
As Servo-Driven fillers, like the Shemesh STRATUM, Mechanical Cam fillers like ASTERRA allow you to programme the filling profile within a single cycle, you can set the filing nozzles to fill quickly initially and then slowly as the bottle shape tapers towards the top – limiting spillage and foaming.
In conclusion – Mechanical Cam liquid filling machinery can do it all!
As you can see from the issues outlined above, there are a number of factors to consider when choosing the right filling mechanism for your new machine.
However, whilst at first the choice may seem overwhelming, one simple fact should help to offer clarity – Mechanical Cam Rotary Piston Fillers can do it all.
Whether you are filling low or ultra-high viscosities, uniform or variably shaped containers at high or low speeds and volumes, Mechanical Cam Rotary Piston Fillers like the ASTERRA can manage the process comfortably while keeping waste to a minimum.
Especially if you are filling ultra-high viscosity products, ASTERRA should be your first port of call.
Most important – Quality Counts!
Mechanical Cam Rotary Piston Fillers are not all created equal, complicating your choice further.
When you choose Shemesh however, you will have the comfort of knowing that we build more than 30 years of engineering expertise into every inch of your liquid filling machinery. The ASTERRA offers the following premium specs and benefits:
- Throughput: Up to 300ppm with the 16 stations ASTERRA model. Faster ASTERRA models available with bigger turrets and up to 72 filling stations.
- Robust and sanitary design construction.
- Mainframes and construction base made of AISI stainless steel 304. All product contact parts are AISI 316 stainless steel or FDA compliant polymer.
- Programmable bottom-up portioning speed graph to adjust for various foaming and viscosities degrees. Drip/Splash/Overflow proprietary prevention mechanisms.
- Controls platform by Siemens or Allen Bradley
- Gears and motors by SEW
- Pneumatics by Festo
- Machine is Industry 4.0 ready
- “No can – no fill” device with anti-breakage safety
- Pistons entirely in stainless steel. Cylinders in high thickness stainless steel.
- No tool removal of pistons and valve plugs
- Explosion proof / Corrosion proof upgrades available
If you would like to talk to our team of engineering experts about your next filling machine, Please contact us today!