Sauce manufacturers know that filling bottles with thick and viscous products like ketchup, mayonnaise and honey for example, can be a challenging process. In this article, we will discuss why servo driven piston fillers are the high ROI packaging machinery solution for sauce manufacturers looking for consistent, efficient, and cost-effective filling solutions.
Advantages of Servo Driven Piston Liquid Fillers for Sauce Manufacturers
Servo driven piston liquid fillers provide several advantages that make them the ideal solution for sauce manufacturers:
Consistency and Precision: If you intend to squeeze every drop of ROI out of your filling machine, keeping waste to an absolute minimum is essential. Servo driven piston fillers offer unparalleled accuracy and precision when filling bottles.
They are specifically engineered to handle a wide range of viscosities – even ultra-thick condiments like Peanut Butter, ensuring that each bottle is filled to the exact same level, resulting in consistent product quality.
Because no two sauces behave exactly the same way during the filling process, the Shemesh STRATUM liquid filling machine utilises servo controls both in the pistons and the nozzles to give manufacturers the ultimate level of control over their filling process – from filling speed to nozzle depth.
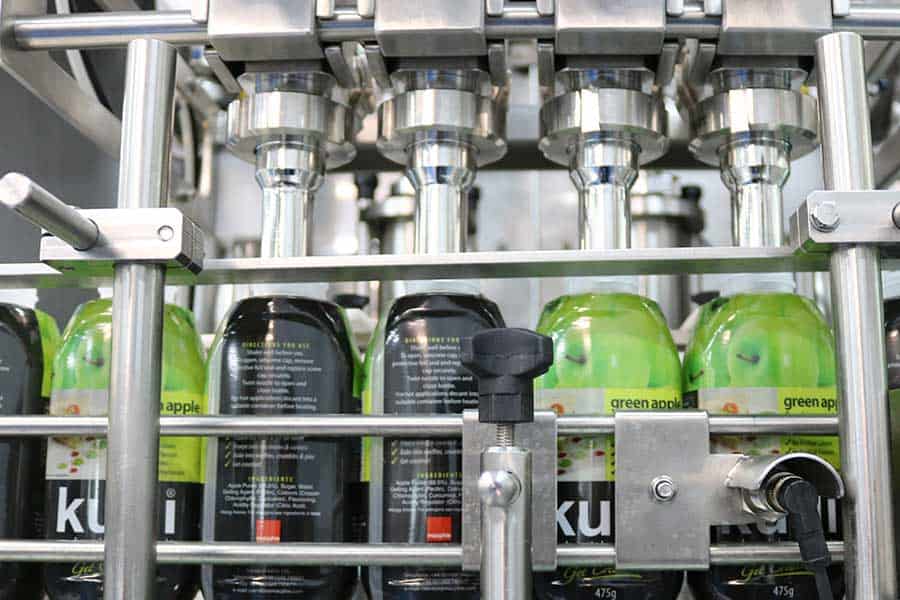
Unlike pneumatic piston fillers where an external air supply is needed – which may vary during the day, servo driven piston fillers don’t rely on any external air supply, so are more consistent and utilise less utilities.
Speed & Efficiency: With servo driven piston fillers, you can fill bottles with viscous sauces quickly and accurately, resulting in increased production rates and reduced waste. These machines are designed to handle a high volume of products, making them ideal for busy sauce manufacturers. Because the servos are electronically controlled via a HMI, you have complete control over the speed of your machine – and you can rely on the servos to keep the speed consistent.
Easy to Clean and Maintain: Servo driven piston fillers are designed with ease of maintenance in mind. The Shemesh STRATUM is easy to clean and sanitize using CIP (clean in place) & WIP (wash in place) methods, ensuring that it is always ready for use.
Versatility: Servo driven piston fillers can handle a wide range of bottle sizes and shapes, making them suitable for a variety of sauce manufacturing applications. They can also handle a variety of product viscosities, making them a versatile solution for sauce manufacturers. The Shemesh STRATUM for example has a viscosity applicable range from 1 to 500,000 Centipoise (water is at 1, peanut butter is at 250,000).
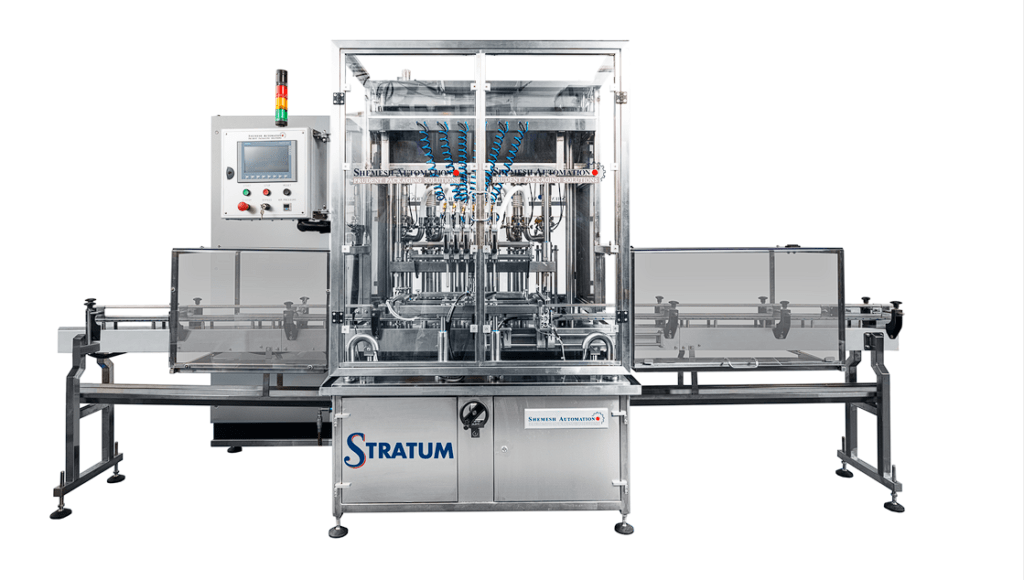
The Shemesh STRATUM Double Servo-Driven Piston Liquid Filling Machine is perfect for viscose sauce filling applications.
Within the Shemesh range, there are also a variety of Servo Driven Piston filling options to suit any application – for example:
- 2-12 stations linear STRATUM: For speeds of 20 – 120ppm
- Dual Lane linear STRATUM: (2 lanes of up to 12 stations each) offering speeds of up to 250ppm thanks to continuous, one lane at a time, filling
- Walking Beam style STRATUM: Offers continuous high-speed filling with no spillages as bottles never stop during the fill process
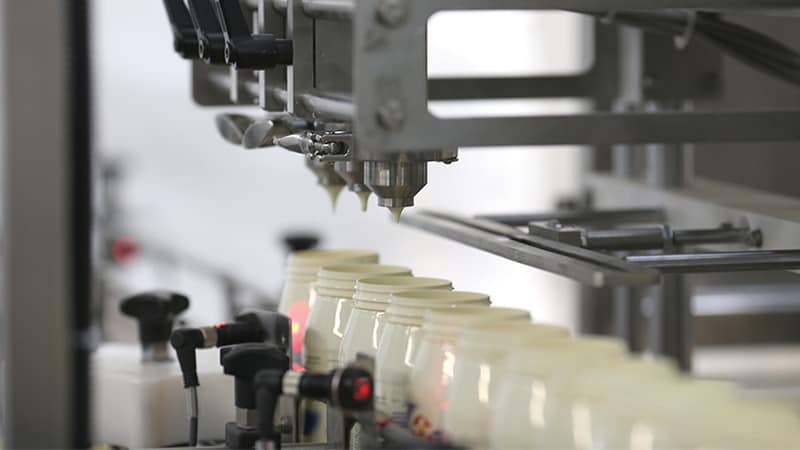
Positive Displacement
Servo-driven piston fillers pack enough punch to positively displace the liquid – meaning that the liquid is forcefully dosed into the container rather than waiting for gravity to do its work (as you would with gravity fillers).
This gain in speed converts to needing fewer nozzles, which reduces the machines overall footprint – saving all important factory space!
For higher throughput requirements Mechanical Cam Rotary Piston Filling machines like the Shemesh ASTERRA also offer the same positive displacement methodology at speeds of over 200ppm.
Another advantage of using mechanical cam rotary piston filling machines is that they suffer less wear and tear because it doesn’t have servo motors and utilities consumption is lower.
Filling Consistency
Pneumatic piston fillers, for example, require an air supply that is external to the machine. This means the quality of filling may vary during any given period as the air supply fluctuates. Servo driven piston fillers on the other hand, have no such requirements, and so are able to offer fully consistent filling throughout the shift regardless of external conditions.
Why Other Types of Liquid Filling Machines are Not as Effective for Sauce Filling
While there are several types of liquid filling machines available on the market, not all of them are effective at filling sauce bottles. Let’s take a look at why other types of liquid filling machines are not as effective at filling bottles with viscous sauces as servo driven piston fillers:
Gravity Fillers: Gravity fillers rely on gravity to fill bottles and are not well-suited for thicker products like ketchup, resulting in inconsistent fills and increased waste.
Pump Fillers: Pump fillers are not as precise as servo driven piston fillers and can be difficult to clean and maintain, leading to decreased efficiency and increased downtime.
Overflow Fillers: Overflow fillers are not suitable for thicker products like ketchup and can result in inconsistent fill volumes and decreased efficiency.
Time-Pressure Fillers: Time-pressure fillers are not as precise as servo driven piston fillers and have a greater risk of inconsistency and decreased product quality.
Net Weight Fillers: Require bottles to be always positioned correctly on the scales during the filling process.
In summary
Servo driven piston fillers offer numerous advantages to sauce manufacturers, including consistency and precision, efficiency, versatility, and easy maintenance – all of which translate to a higher ROI than with other filling methodologies.
Whilst other filling machine methodologies excel at filling other products, when it comes to filling sauce bottles with thick and viscous products like ketchup, honey or mustard, Servo Driven Piston liquid filling machines are our recommendation.
If you are a sauce manufacturer looking for a better filling solution, consider investing in a Servo Driven Piston Filler, like Shemesh’s STRATUM to take your production to the next level. With the right filling machine, you can ensure consistent product quality, increased production rates, and a lower cost per unit.