Traditional production lines have been based around utilising single specialised machines for each distinct process, linked by conveyors and synchronizing systems. For example, a wet wipes packaging line may contain an unwinding unit, a wipes loader, a liquid filling machine, a canister sealing machine, a capper, a labeller and a case packer.
The advantages of this approach are well known: High capacity, high speed and the flexibility to switch product types or machine types when required.
However, advancements in sustainable monoblock (monobloc) technology are offering manufacturers advantages in space and utilities savings, product control and most importantly – cost savings.
Are you missing out on monoblocks (monoblocs)?
What is a monoblock (monobloc)?
Monoblocks (monoblocs) are smart, compact machines that carry out multiple stages of the packaging process in one complete unit.
For example, the Shemesh Sambax is capable of completing the feed, fill, pick & place cap/ overcap and QC functions for small bottles at speeds of up to 100ppm, whilst only taking up approx. 1m x 1.5m in floor space.
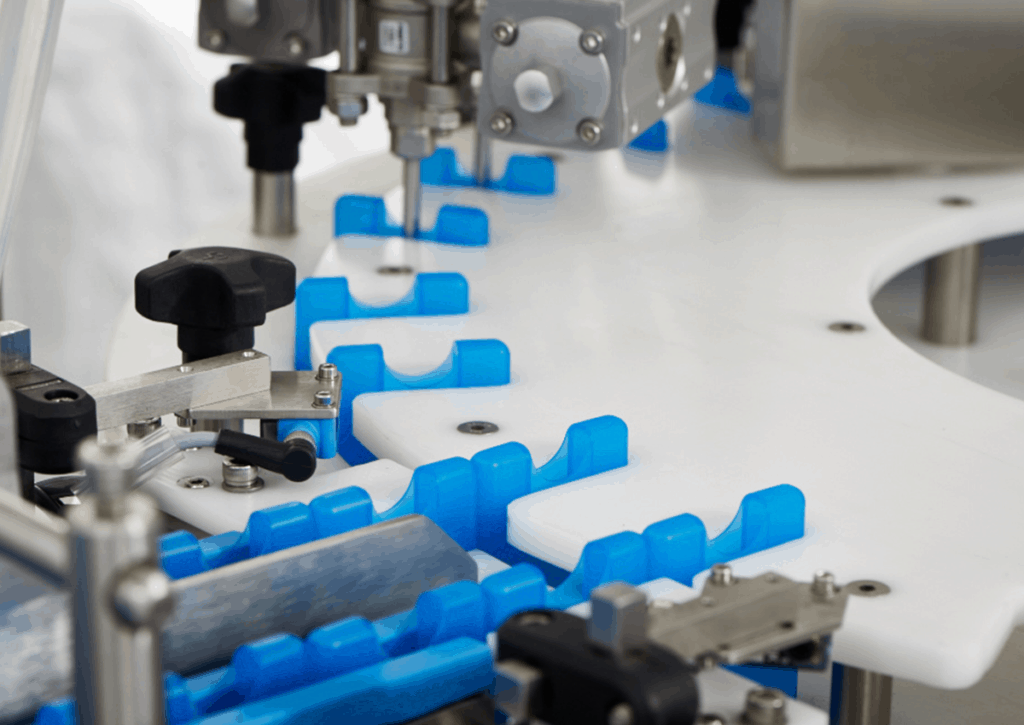
The Shemesh SAMBAX in action
This kind of high-end functionality combined with incredible space and cost savings can translate to real competitive advantage, at a time when global demand is increasing and production capacity is at a premium.
What are the real benefits offered by monoblock (monobloc) solutions?
- Easy synchronisation
With Linear packaging lines, container control is vital. Depending on the size of the line, containers can have a substantial distance to travel from one machine to another.
This leaves plenty of room for error with container positioning, orientation and timing.
Because of this, and the fact that the filling machine, for example, usually operates with a different cadence to the capping machine, synchronisation systems are required to keep lines running like clockwork.
These systems can vary in sophistication from screw feeders and star wheels to sensors and PLC’s – and if yours is not up to scratch, the result could be blockages, downtime and reduced productivity.
With monoblocks (monoblocs) however, products are moved a matter of inches from one station to the next using a simple starwheel and perfect synchronization is achieved using servo motors.
- Space Saving
No manufacturer needs reminding that floorspace is incredibly expensive. Wasting it could mean throwing money down the drain.
With demand for a whole spectrum of products ramping up all over the world, production floor space is at even more of a premium.
That’s where the compact size of monoblocks (monoblocs) could give manufacturers a competitive advantage, leaving room to upscale production capacity at short notice, without wasting time and money on securing additional floorspace.
For example, Shemesh’s CITADEL, a monoblock (monobloc) which undertakes the complete packaging process for wet wipes in flexible packs (35ppm) from bag opening and wipes roll loading to wetting, sealing and QC has a compact footprint of 1.8m x 1.8m.
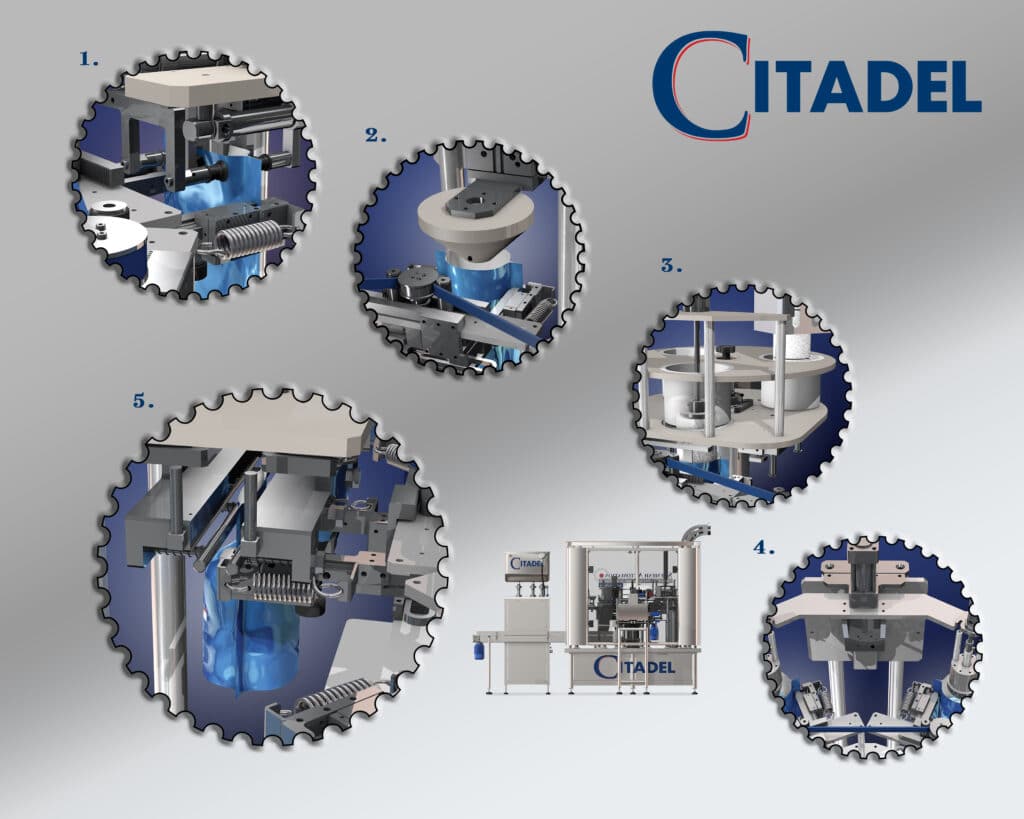
Linear machines fulfilling only the liquid filling portion of the process can easily take up more floor space alone – before conveyors are even factored in.
3) Cost
If monoblock (monobloc) packers can meet your speed demands and your functionality requirements are not subject to constant change then you can unlock huge cost savings by opting for a monoblock (monobloc) packer over an inline system.
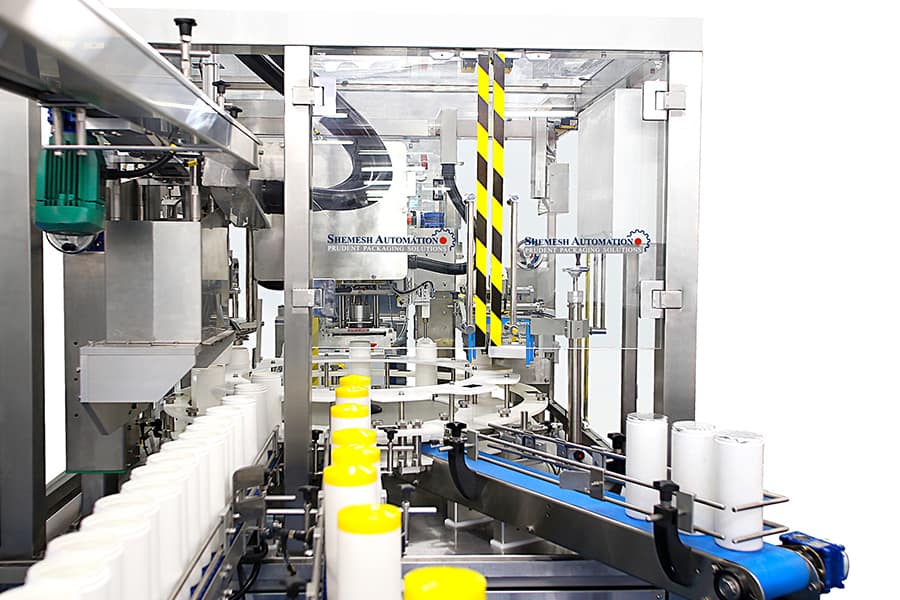
The XPANDER is a compact sustainable solution for the complete packing of canister wipes
For example, Shemesh’s Xpander complete monoblock (monobloc) packer for round wipes in canisters – whilst being a proven ‘best in class’ solution for canister wipes manufacturers all over the world- also costs around 30% of the price of an inline solution for the same product.
Food for thought.
4) Sustainability
It’s not only your bottom line that can benefit from monoblock (monobloc) technology – the environment will too. A move towards smaller, more specialised machinery means a reduced footprint both in terms of physical space, and carbon. monoblocs generally use less electricity and water than linear solutions too, reducing the environmental impact of your production.
For high throughputs and narrow product ranges, it’s fine to stay inline
If you need to run just one product or a narrow range of products at high volumes, it’s likely that an inline solution is still the way to go.
Because you don’t need to make any/many product changeovers, you can afford to let these high-performance lines do what they do best – run run run!
One big advantage of modular lines (or inline solutions) is that they can evolve with your production needs. If you suddenly need to raise your throughput or add functionality to the line you can always replace single machines with faster ones or add additional machines. Monoblocks (monoblocs) however, are “fixed” solutions which cannot be easily changed – it definitely pays to think ahead!
If you need help deciphering which is the right packaging solution for you, don’t hesitate to contact one of our experts: sales@shemeshautomation.com